Conventional rotary molding of plastic parts often requires the use of industrial facilities, making the process expensive and inefficient for small production runs. Additionally, the conventional process creates hollow parts with even thickness around the perimeter. This project explores how custom rotations of a mold using a robotic arm can produce multiple parts with varying thicknesses or shapes from the same mold. This allows the flexibility to create a variety of parts, in small or large quantities.
Due to temporary limitations of the school’s shop facilities at the time, we did not have access to a robot. In turn, we created a plywood rolling jig that allowed specific rotation patterns of a mold, and used a quick-setting thermoset resin as a molding material. After learning from the small scale prototypes, we speculate how the process can be scaled up to create a large scale inhabitable assembly system.
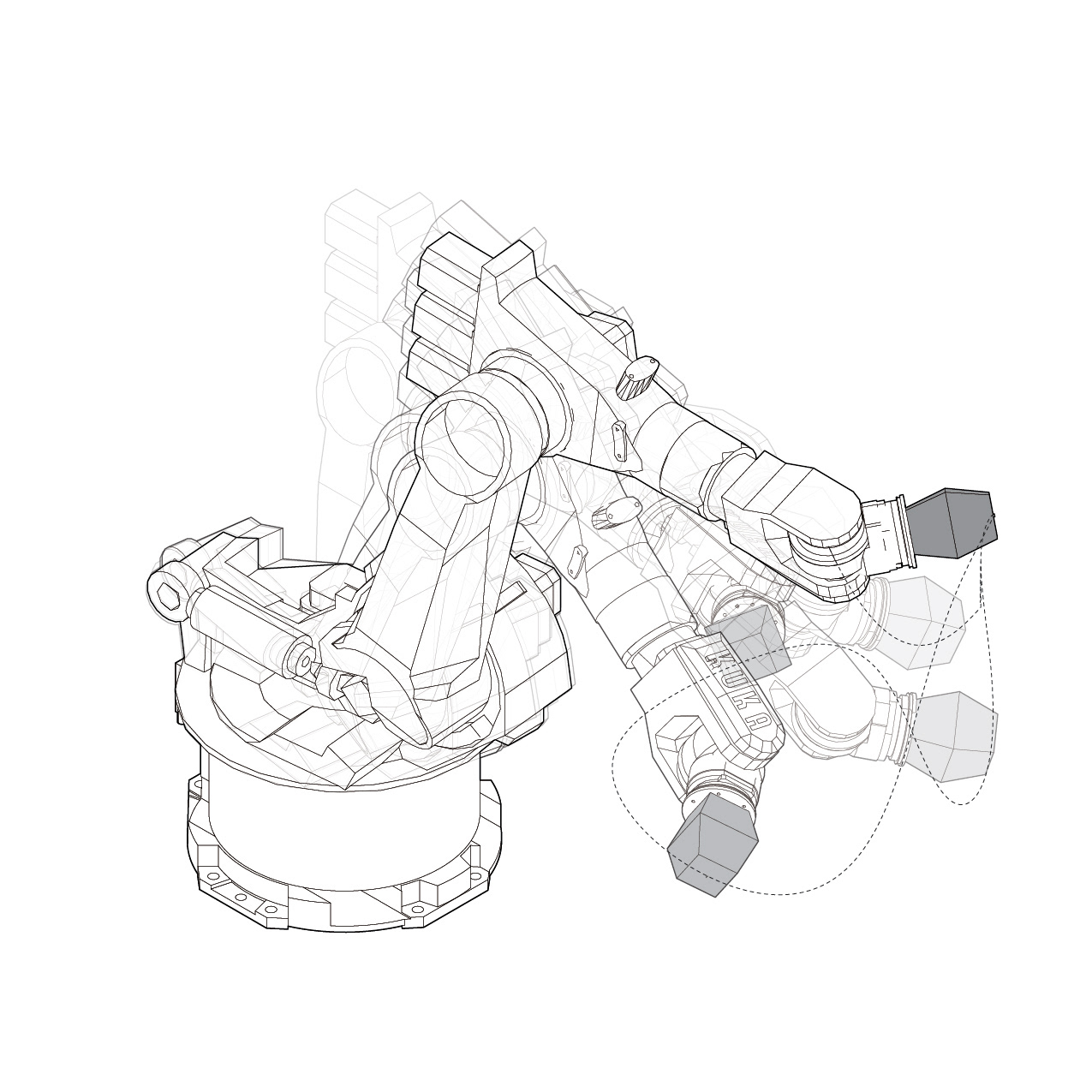
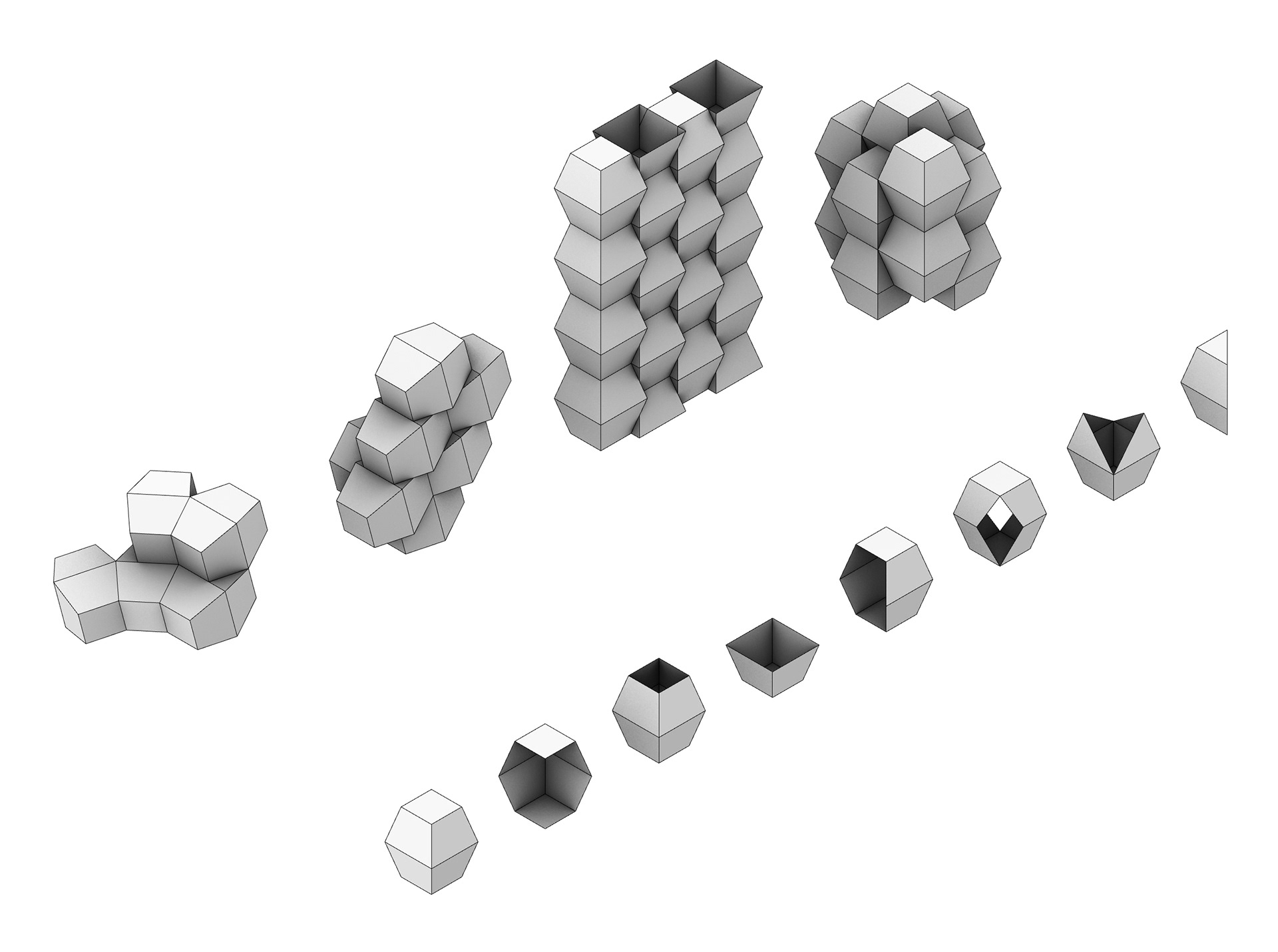
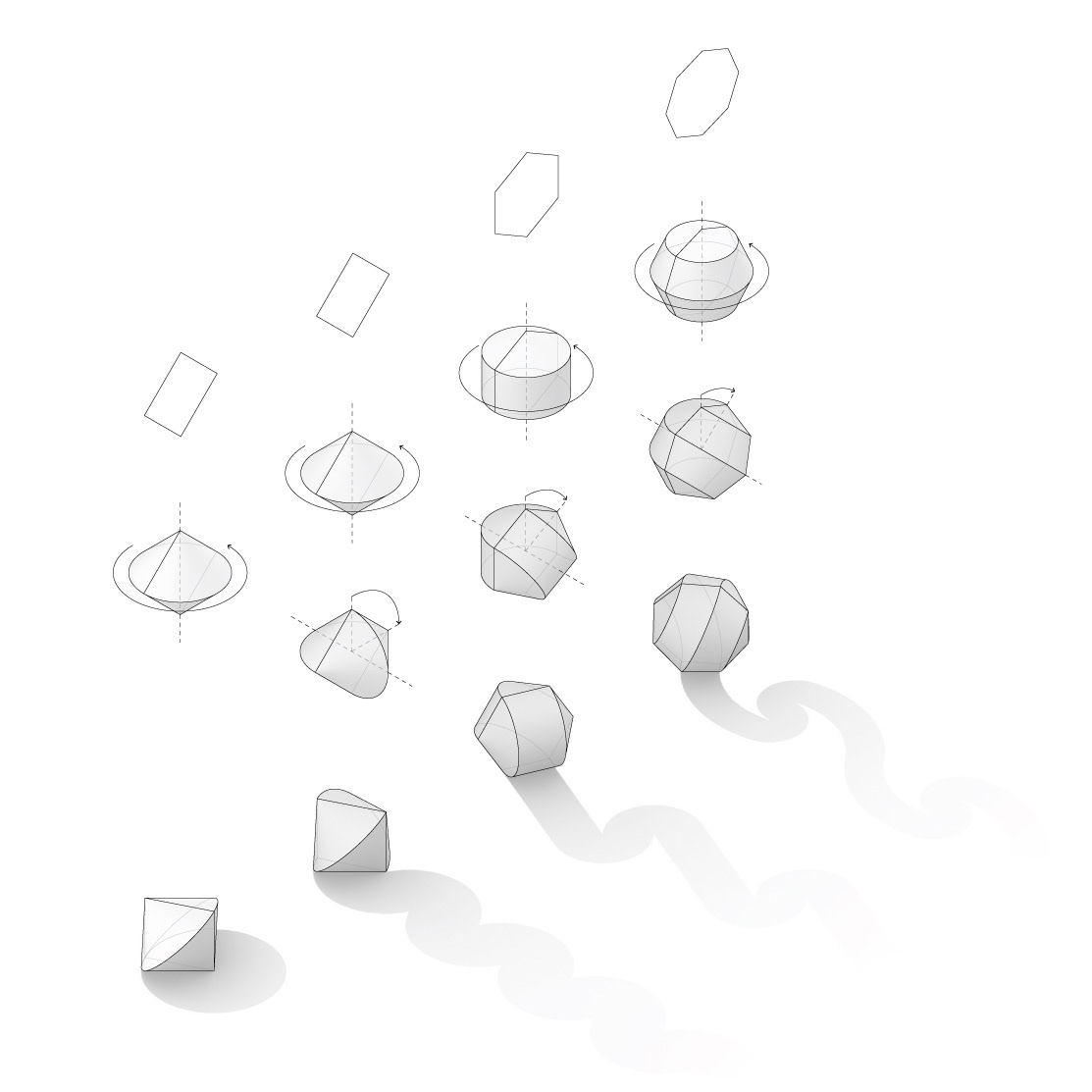
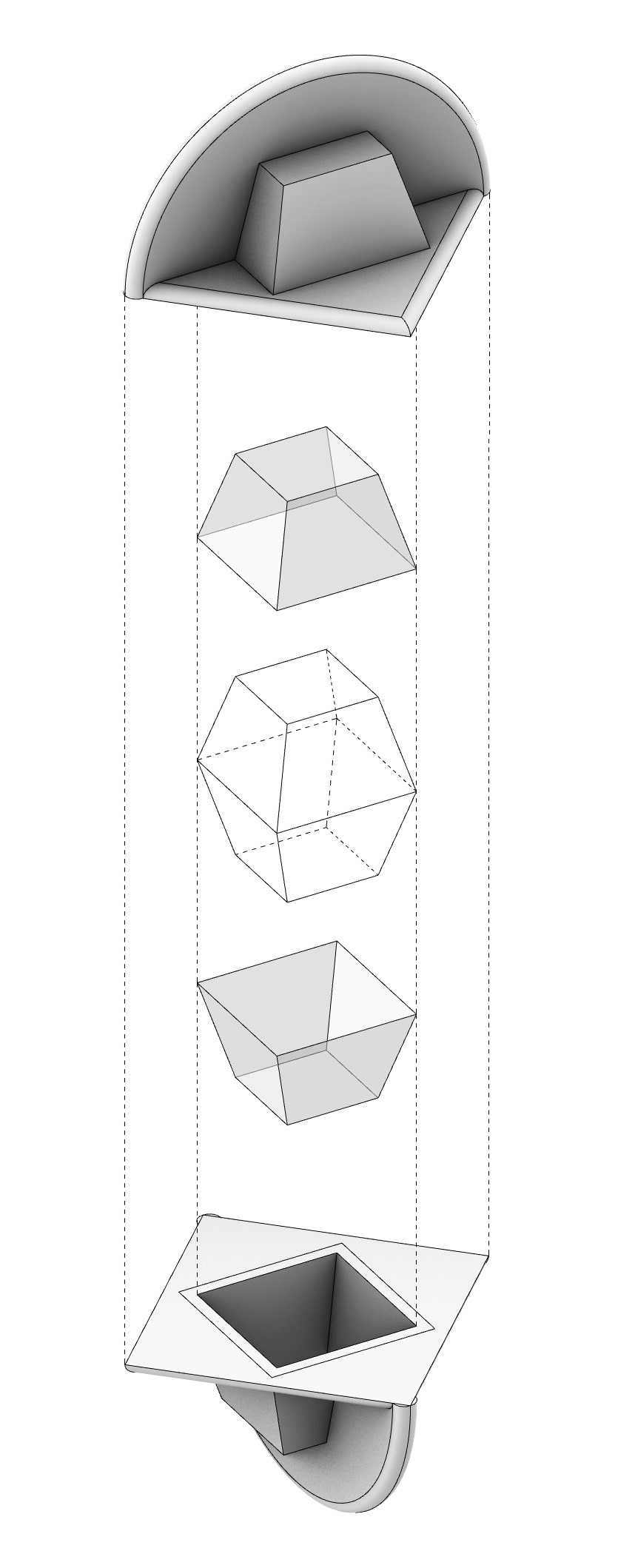
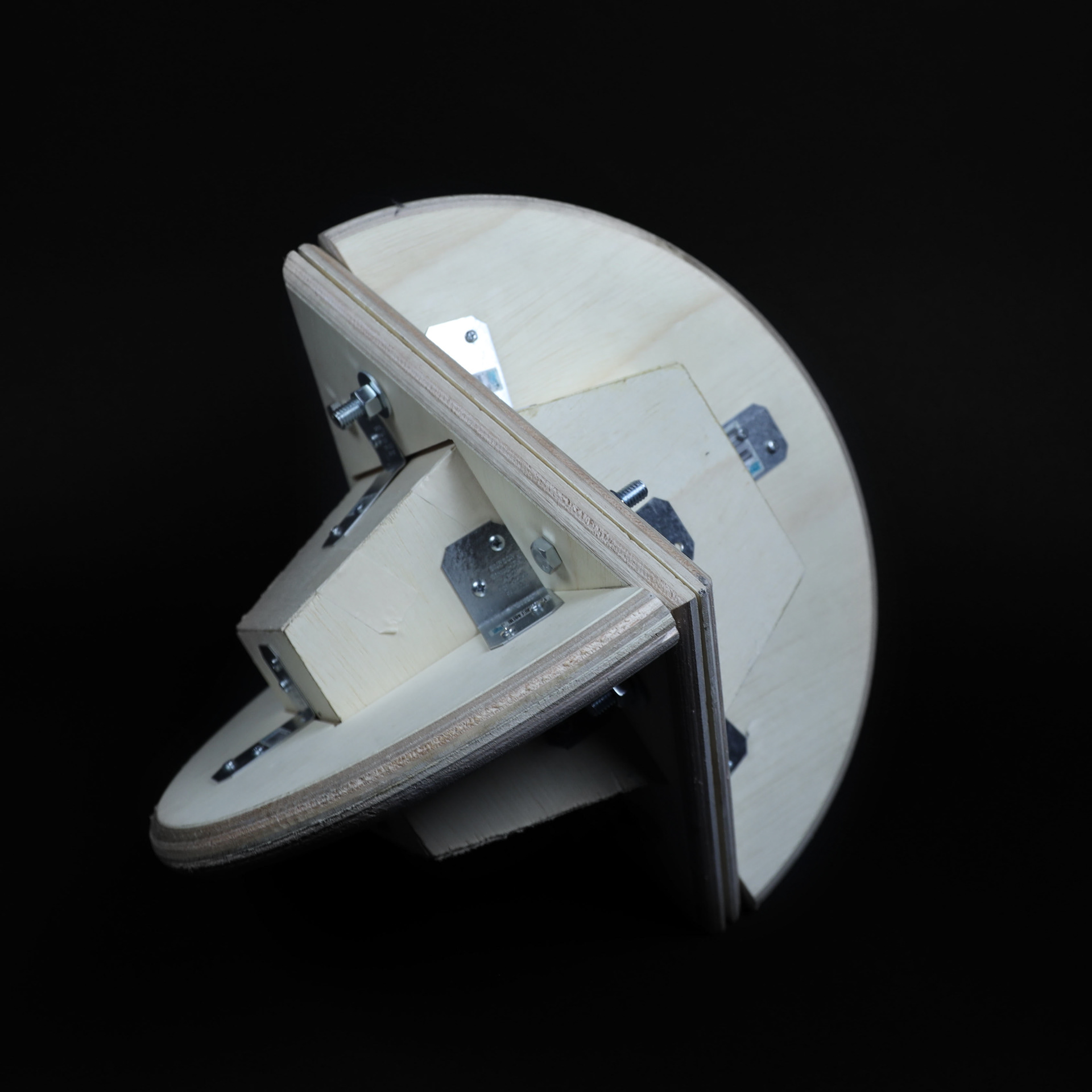
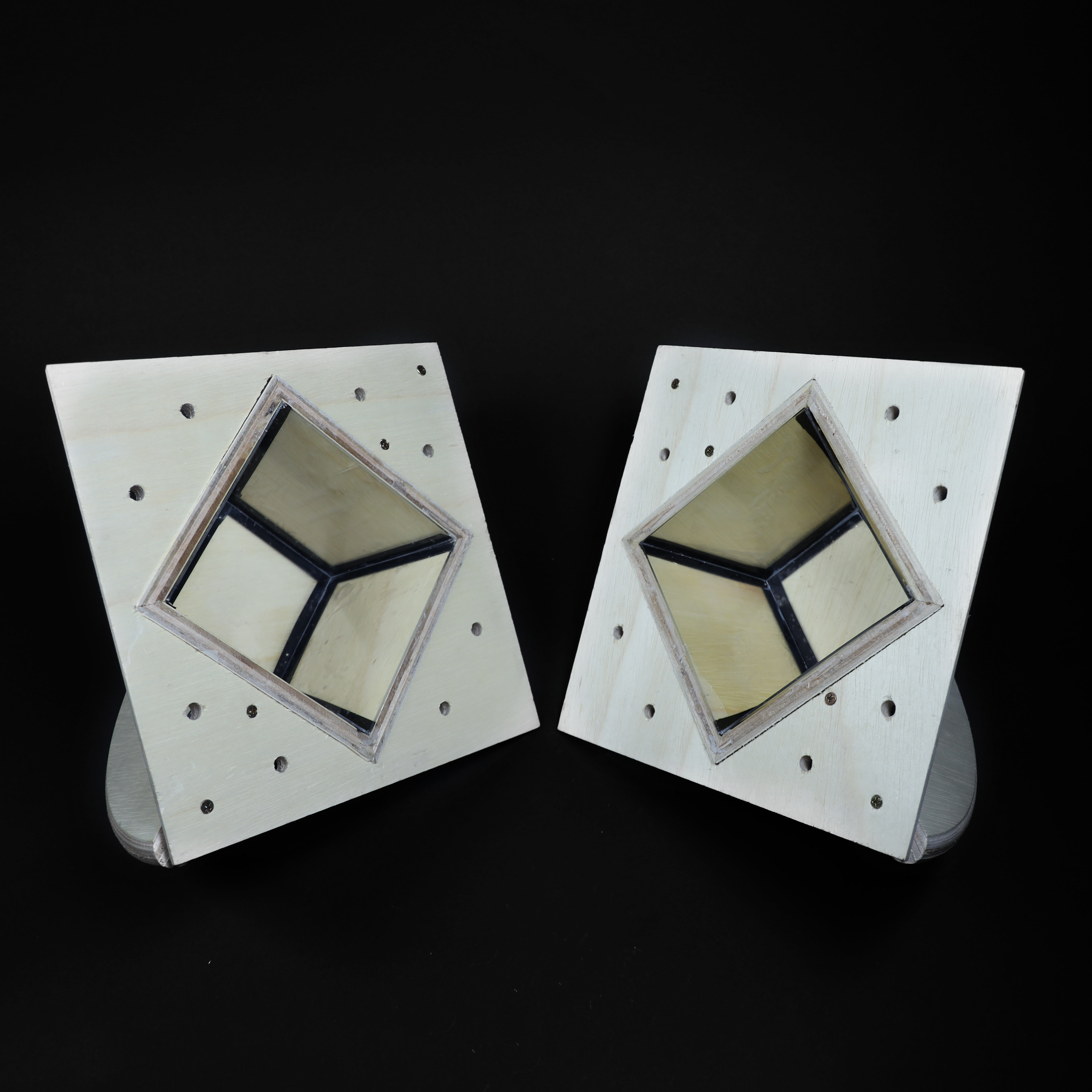
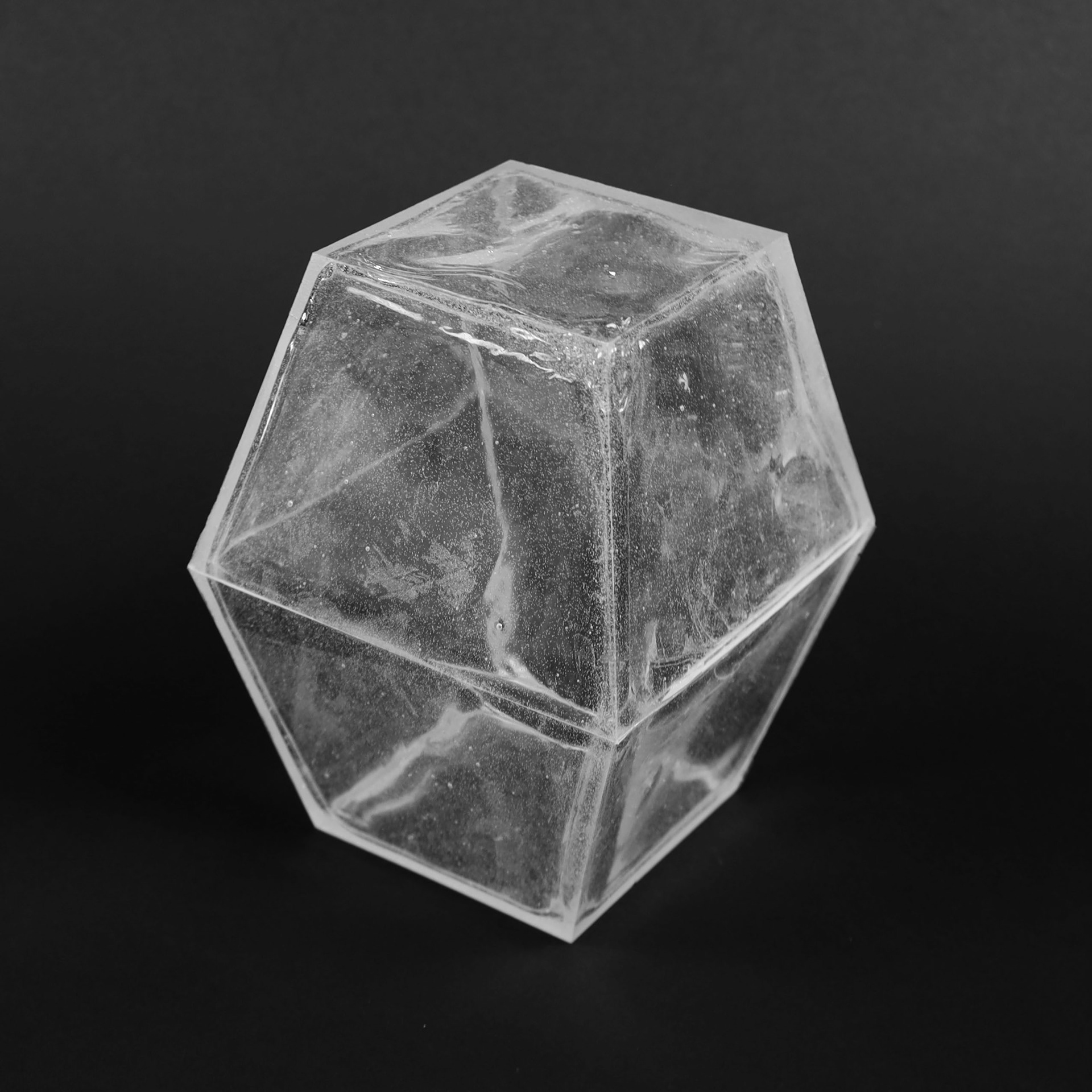
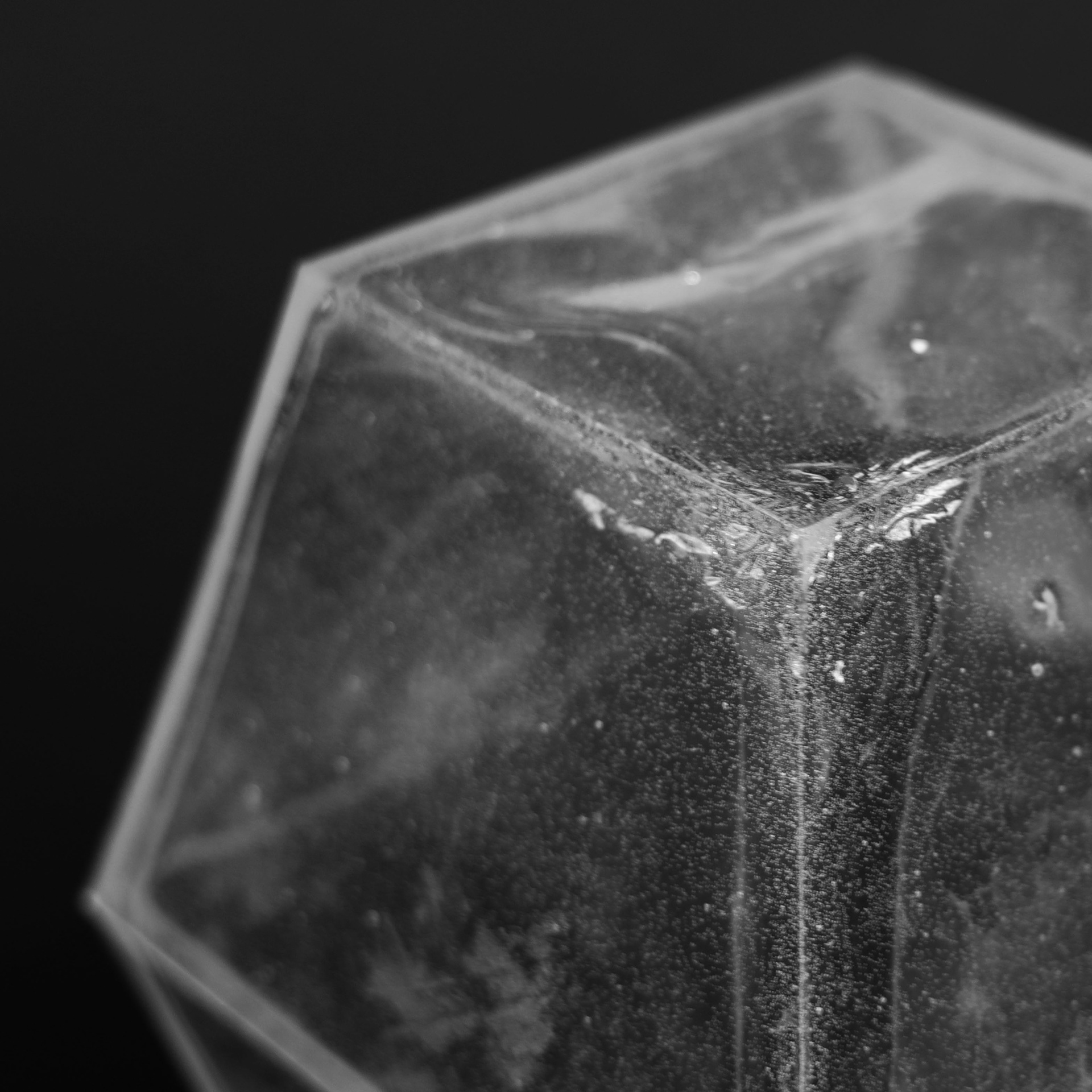
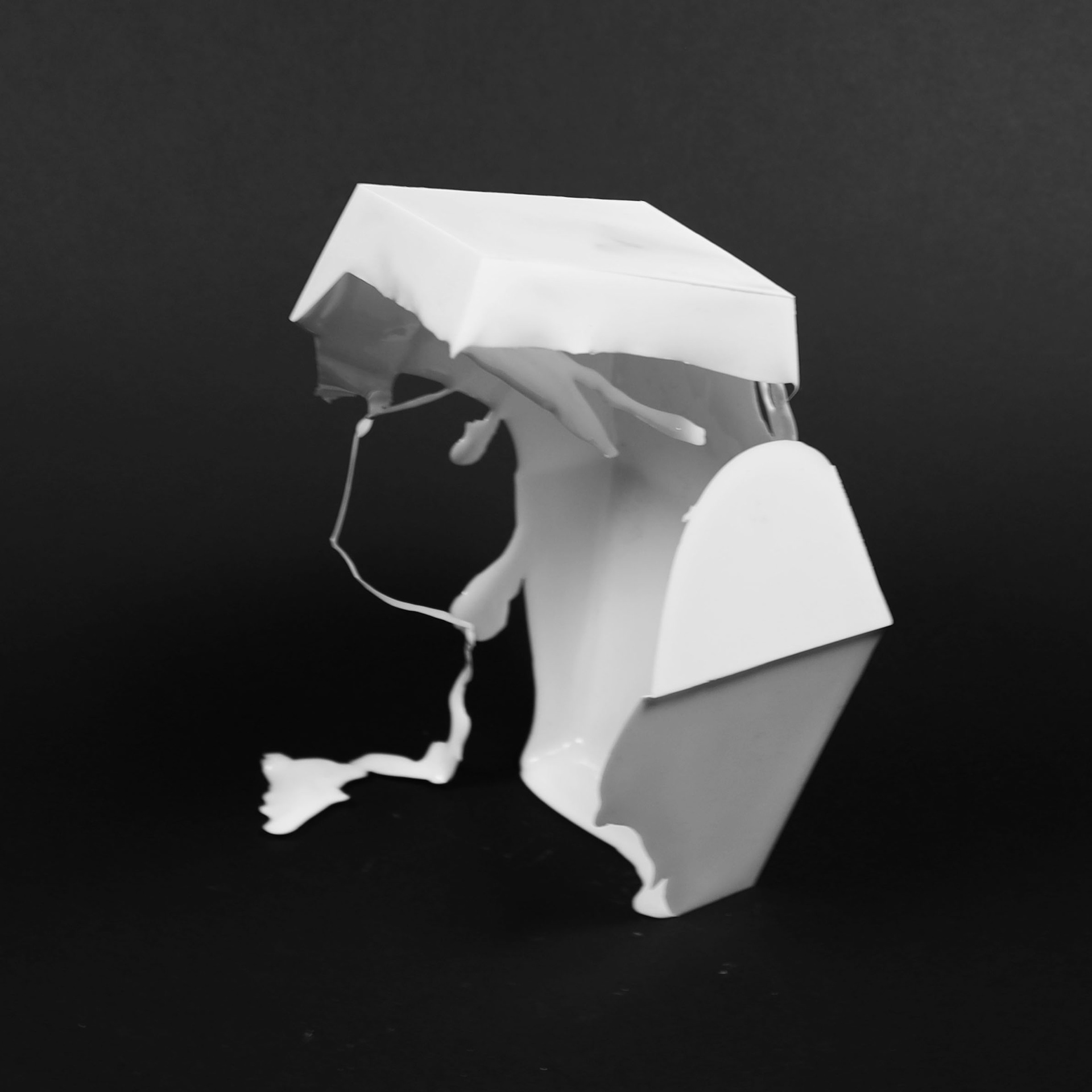
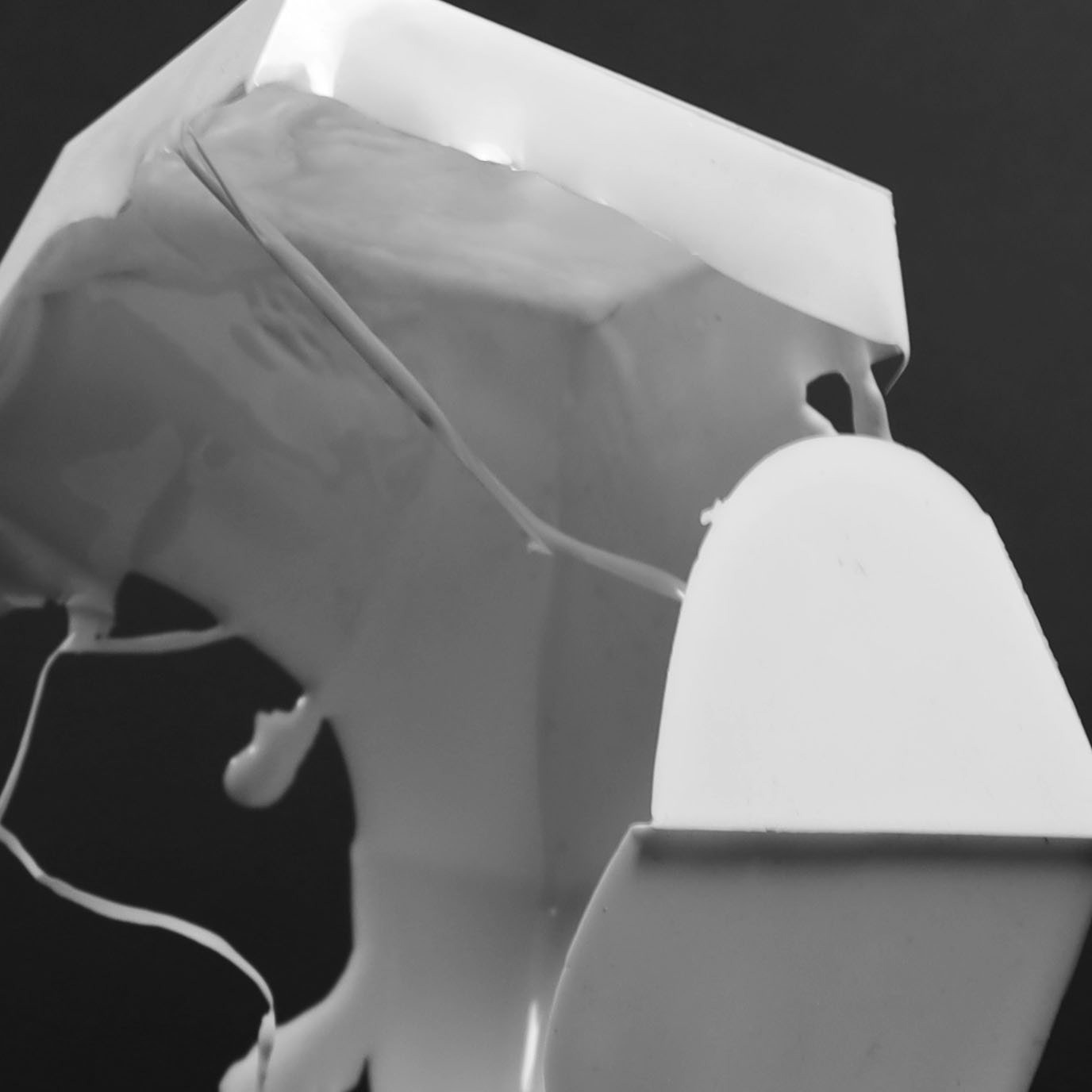
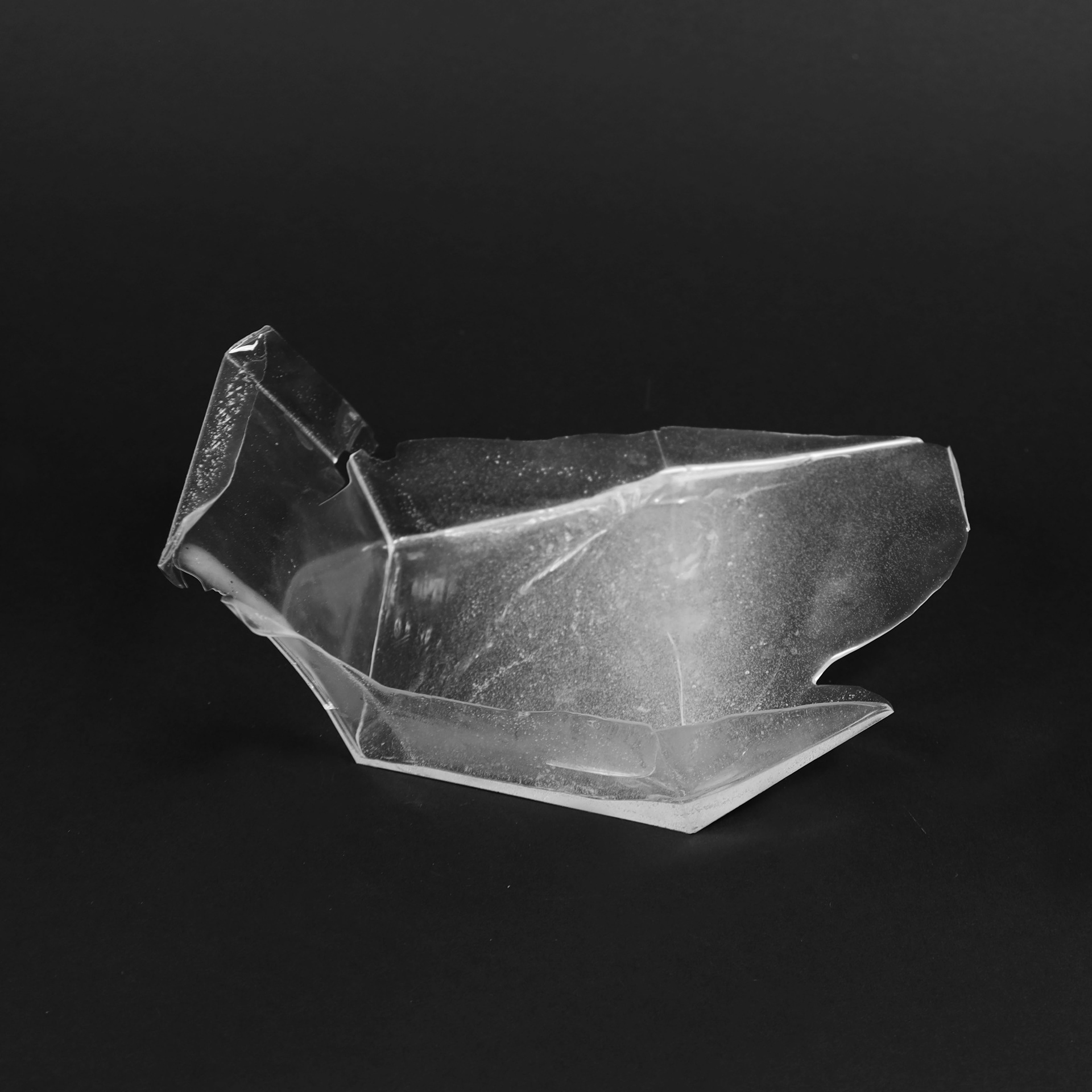
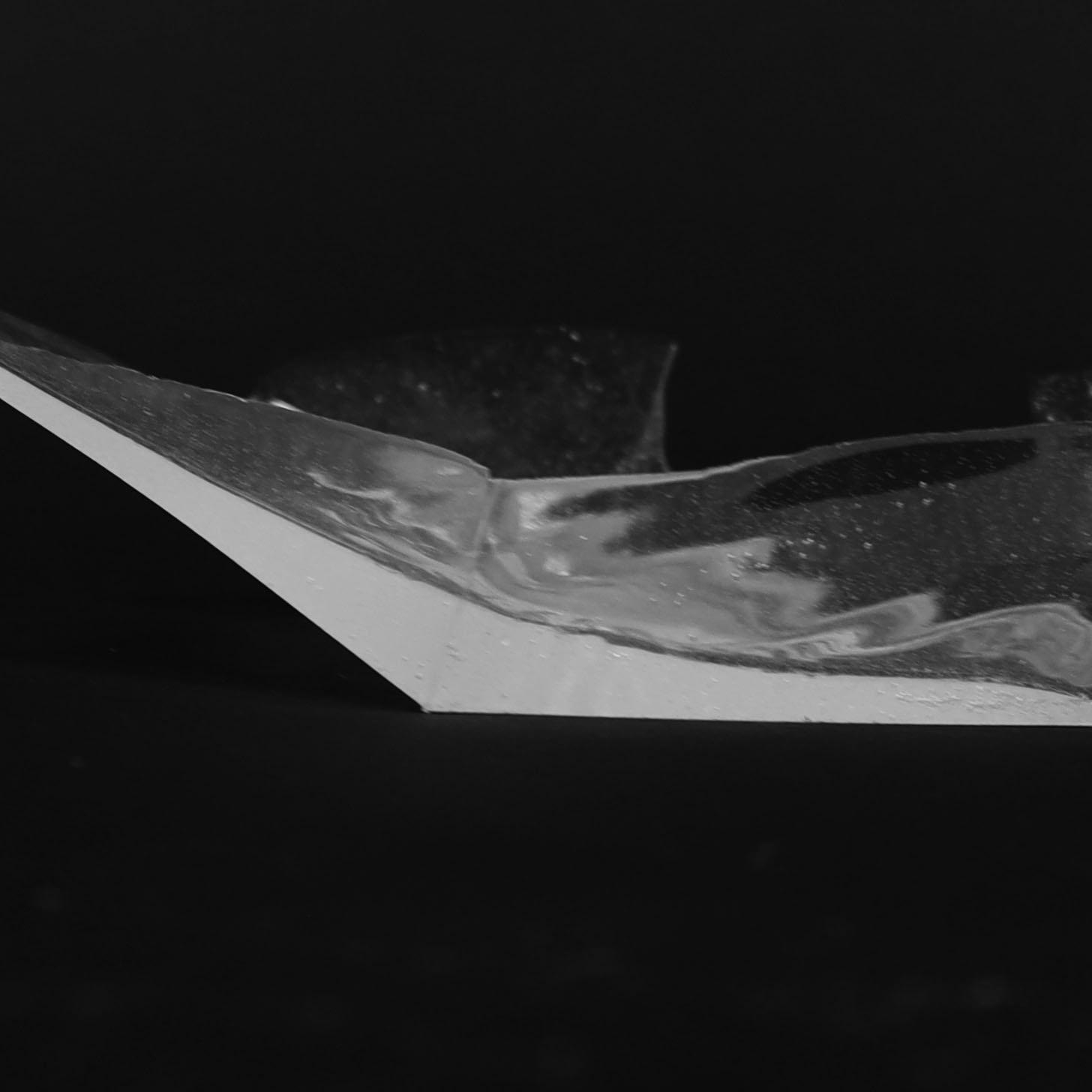
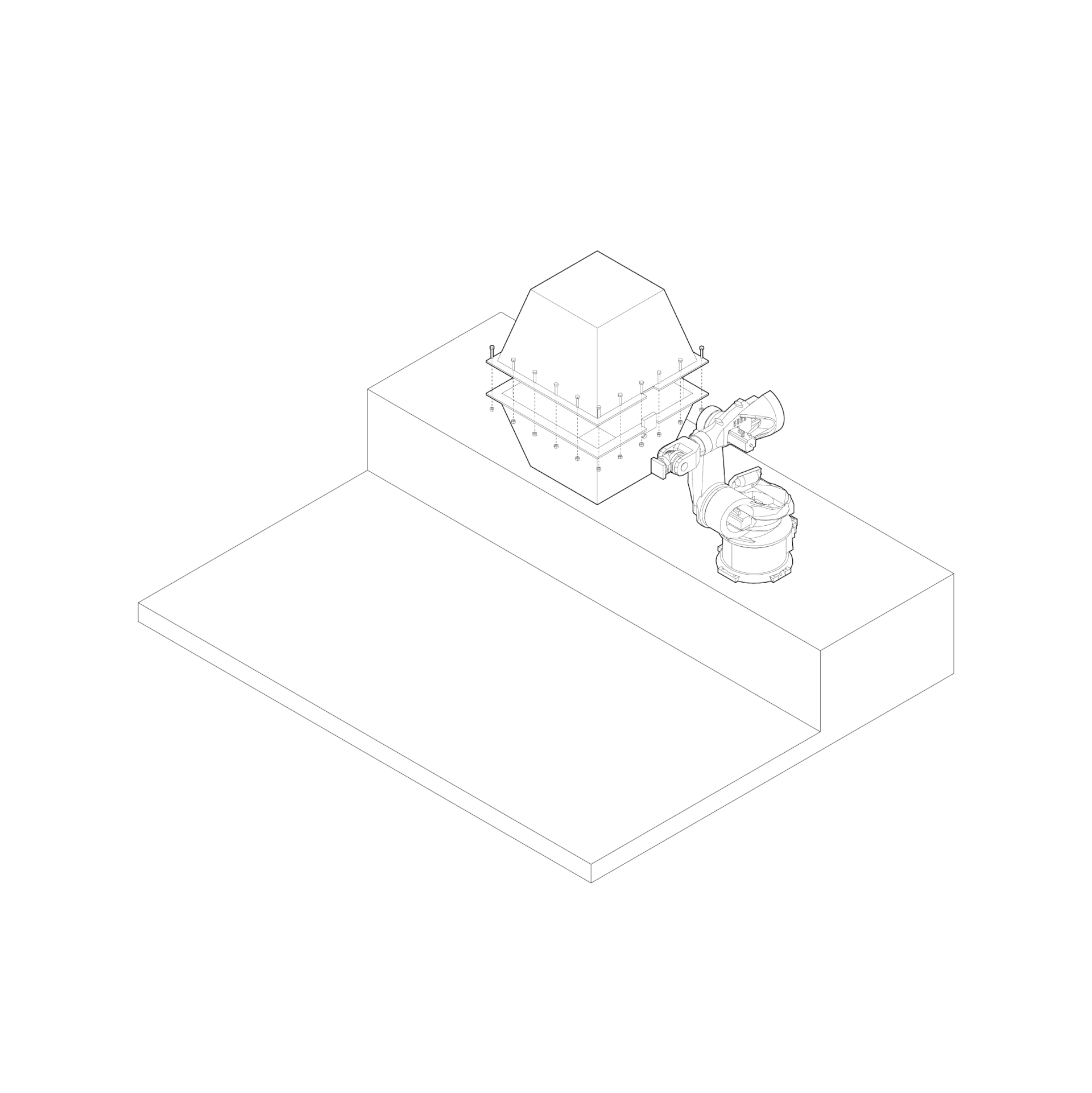

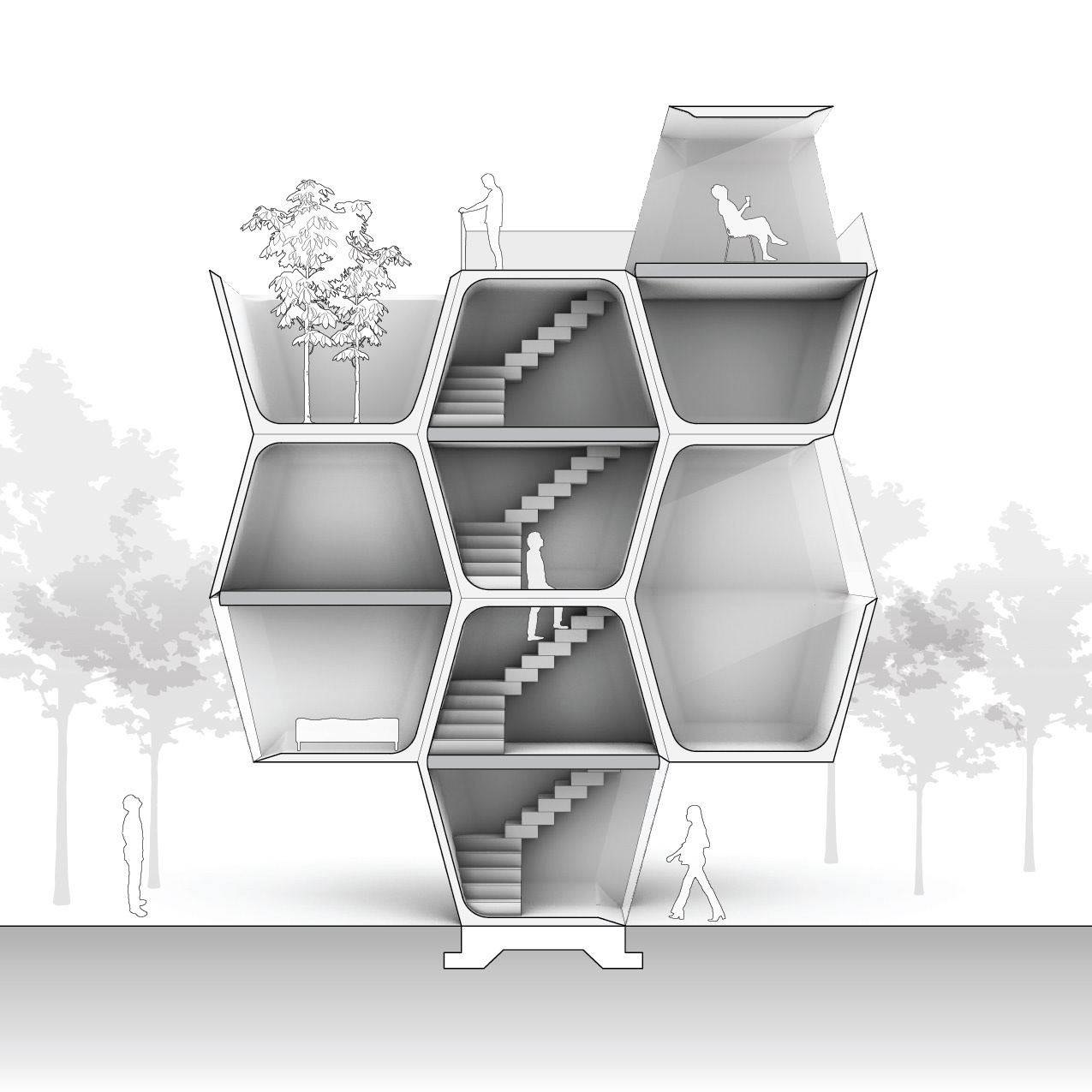